Reassembly1. Install the damper unit on a spring compressor.2. Assemble the damper in reverse order of removalexcept the damper mounting washer and self-locking nut.NOTE: Align the bottom of damper spring and spr-ing lower seat as shown.3. Position the damper mounting base on the damperunit as shown.NOTE: Follow the manufacturer’s instructions.LEFT Front RIGHTUpper view17°30′ ± 3°Bracketposition18°30′ […]
nsxb18029a.pdf
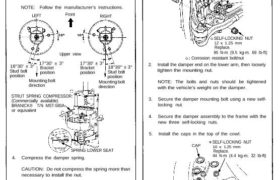