Category: Clutch
nsxb12005a.pdf
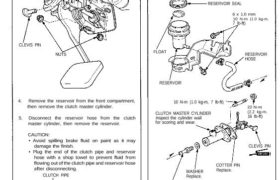
Clutch Master Cylinder Removal 1. Disconnect the clutch pipe from the clutch master cylinder. 2. Pry out the cotter pin, and pull the clevis pin out of the clevis. 3. Remove the nuts. COTTER PIN Replace. CLEVIS PIN 4. Remove the reservoir from the front compartment, then remove the clutch master cylinder. 5. Disconnect the […]
nsxb12017a.pdf
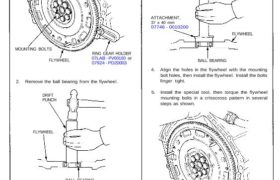
Replacement 1. Remove the flywheel mounting bolts in a criss- cross pattern in several steps, and remove the flywheel. MOUNTING BOLTS FLYWHEEL RING GEAR HOLDER 07LAB – PV00100 or 07924 – PD20003 2. Remove the ball bearing from the flywheel. DRIFT PUNCH FLYWHEEL BALL BEARING 3. Drive the new ball bearing into the flywheel using […]
nsxb12011a.pdf
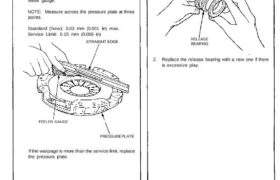
Pressure Plate Inspection NOTE: If replacement is required, always replace the pressure plate, mid plate, and flywheel as a set. 1. Inspect the pressure plate surface for wear, cracks, and burning. 2. Inspect the fingers of the diaphragm spring for wear at the release bearing contact area. 3. Inspect for warpage using a straight edge […]
nsxb12013a.pdf
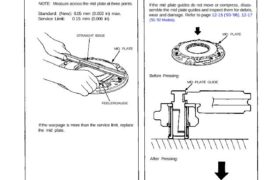
Mid Plate Inspection NOTE: If replacement is required, always replace the pressure plate, mid plate, and flywheel as a set. 1. Inspect the mid plate surface for wear, cracks, and burning. 2. Inspect for warpage using a straight edge and feeler gauge. NOTE: Measure across the mid plate at three points. Standard: (New): 0.05 mm […]
nsxb12006a.pdf
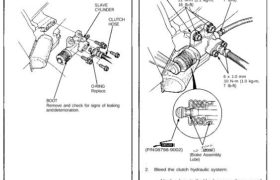
Slave Cylinder Removal 1. Disconnect the clutch hose from the slave cylinder. CAUTION: • Avoid spilling brake fluid on the painted sur- faces, as it may damage the finish. • Plug the end of the clutch hose with a shop towel to prevent brake fluid from coming out. 2. Remove the slave cylinder from the […]
nsxb12002a.pdf
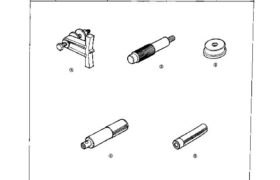
Special Tools Ref.No. Tool Number 07LAB — PV00100 or 07924 — PD20003 07MAF—PR80100 07746 — 0010200 07749 — 0010000 07936 — 3710100 Description Ring Gear Holder Clutch Alignment Shaft Attachment, 37 x 40 mm Driver Handle Qty Page Reference 12-10, 17, 18, 19 12-18, 19 12-17 12-17 12-18, 19 1 1 1 1 1 Attachments […]
nsxb12008a.pdf
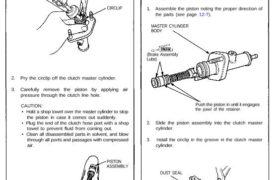
Clutch Master Cylinder (Canada) Disassembly CAUTION: Avoid spilling brake fluid on paint as it may damage the finish. 1. Remove the dust seal from the clutch master cylinder. DUST SEAL CIRCLIP 2. Pry the circlip off the clutch master cylinder. 3. Carefully remove the piston by applying air pressure through the clutch line hole. CAUTION: […]
nsxb12003a.pdf
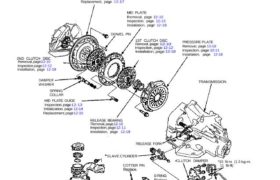
Illustrated Index NOTE: Whenever the transmission is removed, clean and grease the release bearing sliding surface. If the parts marked * are removed, the clutch hydraulic system must be bled. Bleed the clutch hydraulic system (see page 12-6). Inspect the hoses for damage, leaks, interference, and twisting. FLYWHEEL Inspection, page 12-16 Replacement, page 12-17 MID […]
nsxb12018a.pdf
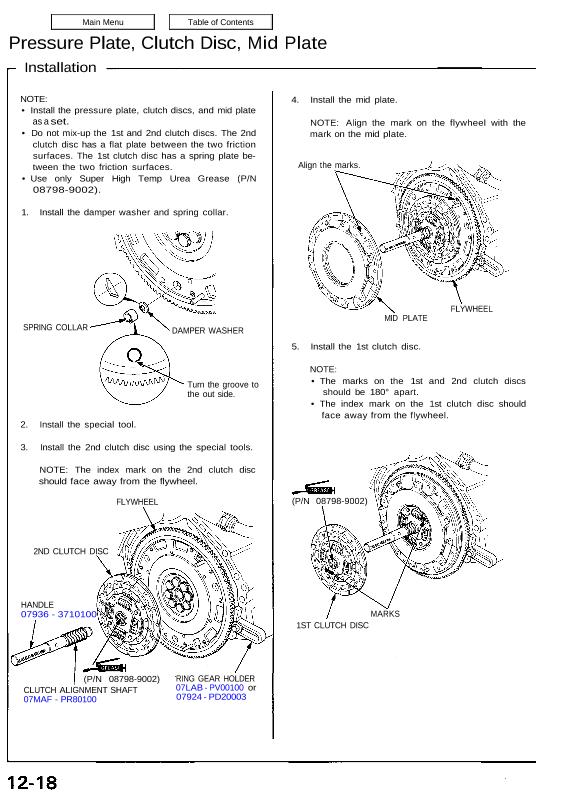
Pressure Plate, Clutch Disc, Mid Plate Installation NOTE: • Install the pressure plate, clutch discs, and mid plate as a set. • Do not mix-up the 1st and 2nd clutch discs. The 2nd clutch disc has a flat plate between the two friction surfaces. The 1st clutch disc has a spring plate be- tween the […]
nsxb12014a.pdf
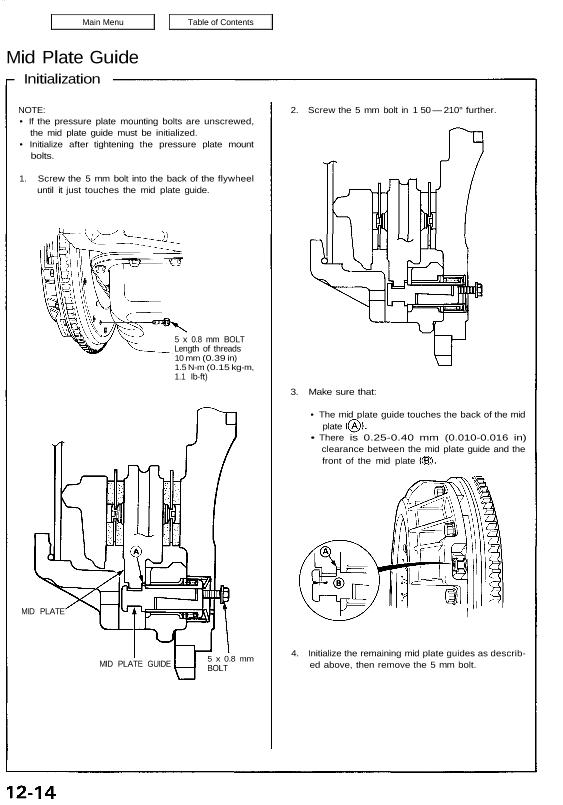
Mid Plate Guide Initialization NOTE: • If the pressure plate mounting bolts are unscrewed, the mid plate guide must be initialized. • Initialize after tightening the pressure plate mount bolts. 1. Screw the 5 mm bolt into the back of the flywheel until it just touches the mid plate guide. 5 x 0.8 mm BOLT […]