Category: Construction & Function
nsxd05013a.pdf
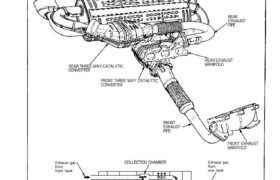
Exhaust System Dual Exhaust System A compact dual exhaust system is used to provide low back pressure. Sound tuning has been optimized to give a sporty exhaust sound note suitable to this type of car. This is done by a col- lection chamber in muffler. MUFFLER REAR EXHAUST PIPE REAR EXHAUST MANIFOLD FRONT THREE WAY […]
nsxd05011a.pdf
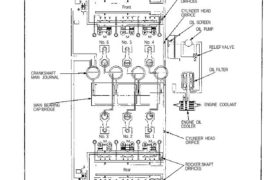
Lubrication System Lubrication Flow VTEC SOLENOID VALVE ROCKER SHAFT ORIFICES M M M CYLINDER HEAD ORIFICE OIL SCREEN OIL PUMP RELIEF VALVE OIL FILTER ENGINE COOLANT ENGINE OIL COOLER CYLINDER HEAD ORIFICE ROCKER SHAFT ORIFICES P: PRIMARY M: MID S: SECONDARY M M M VTEC SOLENOID VALVE No. 3 M M M No. 1No. 2 […]
nsxb05011a.pdf
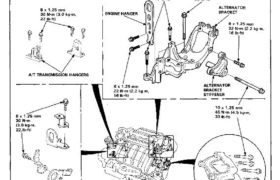
Installation Additional Torque Value Specifications: NOTE: For manifold replacement, refer to section 9. Engine Removal/Installation Engine Removal/Installation Installation Engine Installation: Install the engine in the reverse order of removal. Reinstall the mount bolts/nuts in the following sequence, failure to follow these procedures may cause excessive noise and vibration, and reduce bushing life. 1. Install the […]
nsxd05004a.pdf
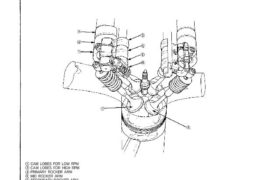
Variable Valve Timing and Valve Lift Electronic Control System (VTEC) Outline The engine is equipped with multiple cam lobes per cylinder, providing one valve timing and lift profile at low speed and a different profile at high speed. Switch-over from one profile to the other is controlled electronially, and is selected by monitoring current engine […]
nsxd05019a.pdf

Engine Removal/Installation Make sure jacks and safety stands are placed proper- ly and hoist brackets are attached to the correct positions on the engine (see section 1). Make sure the car will not roll off stands and fall while you are working under it. 3. Remove the expansion tank cap to speed draining. Use care […]
nsxb05002a.pdf
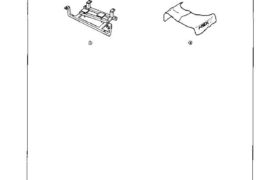
Special Tools Ref. No. Tool Number 07MAK – PR7020A 07MAZ – SL0000A Description Engine Removal/Installation Fixture NSX Fender Cover Qty 1 1 Page Reference 5-9 (’91-’93 Models) ,or (’94-’96 Models) 5-3 (’91-’93 Models) ,or (’94-’96 Models) Attachments nsxb05002a (34 kB)
nsxb05003a.pdf
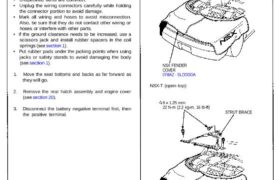
Engine Removal/Installation Removal Make sure jacks and safety stands are placed properly and hoist brackets are attached to the correct posi- tions on the engine (see section 1). • Make sure the car will not roll off stands and fall while you are working under it. CAUTION: • Use a fender cover (special tool) to […]
nsxd05014a.pdf

Cooling Cooling System Two cooling systems are employed: An antifreeze/water system with the radiator mounted in the front of the vehicle. An air-cooling system driven by a fan mounted in the engine compartment. BLEEDER RADIATOR BLEEDER WATER VALVE HEATER CORE DRAIN DRAINS BLEEDER ENGINE DRAIN WATER PUMP ENGINE OIL COOLER ENGINE DRAIN FAST IDLE THERMO […]
nsxd05018a.pdf
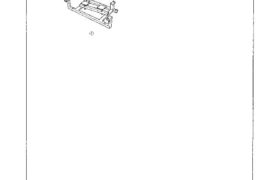
Special Tools Ref. No. Tool Number 07MAK-PR7020A Description Engine Removal/Installation Fixture Qty 1 Page Reference 5-27 Main Menu Table of Contents Special Tools Ref. No. Tool Number Description ł Qty Page Reference ® 07MAK—PR7020A Engine Removal/Installation Fixture 1 5-27 5-18 Attachments nsxd05018a (48 kB)
nsxd05029a.pdf
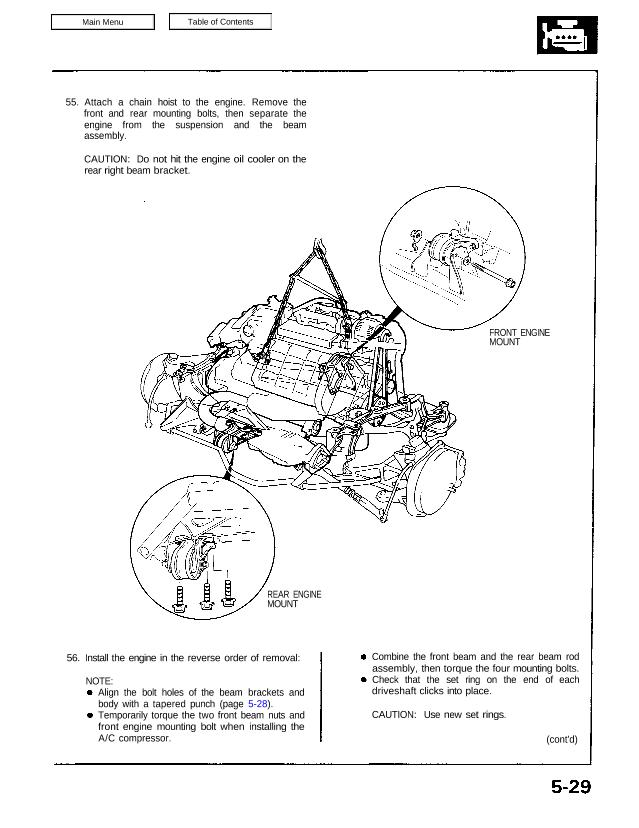
55. Attach a chain hoist to the engine. Remove the front and rear mounting bolts, then separate the engine from the suspension and the beam assembly. CAUTION: Do not hit the engine oil cooler on the rear right beam bracket. FRONT ENGINE MOUNT REAR ENGINE MOUNT 56. Install the engine in the reverse order of […]