Category: Brakes & ABS
nsxd19076a.pdf
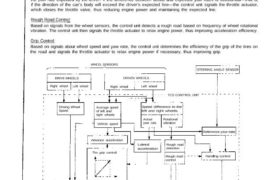
System Description TCS Control unit Acceleration Control: The TCS control unit gets signals from the wheel sensors about the rotational speed of each wheel. Traction control is activated when the rotational speed of the driving wheels differs from the rotational speed of the driven wheels (i.e., vehicle speed). Handling Control: Based on signals about driving […]
nsxb19082a.pdf
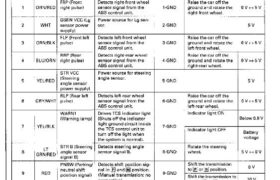
TCS Control Unit Terminal Arrangement Main Menu Table of Contents TCS Control Unit Terminal Arrangement TCS CONTROL UNIT 14P CONNECTOR | 1 2 3 Q | 4 5 6 7 8 91011l121314 ‚Ир CONNECTOR WIRE SIDE OF FEMALE TERMINALS Voltage Terminal Wire Terminal sign . . „umher ook” (Termina name) Descr’pt’on Measurement Conditions Output terminals […]
nsxb19070a.pdf
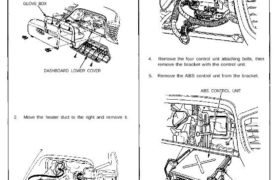
ABS Control Unit Replacement SRS components are located in this area. Review the SRS component locations, precautions, and procedures in the SRS section 24 before performing repairs or service. 1. Remove the dashboard lower cover and glove box, and disconnect the light connector. GLOVE BOX DASHBOARD LOWER COVER 2. Move the heater duct to the […]
nsxb19107a.pdf
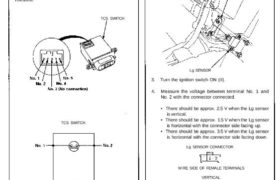
Electronic Components TCS Switch Inspection Between terminal No. 4 and No. 5 (Illumination light circuit) There should be continuity. Between terminal No. 1 and No. 2 (Switch circuit) There should be continuity when the switch is pushed, and there should be no continuity when the switch is released. TCS SWITCH TCS SWITCH Lateral Acceleration (Lg) […]
nsxb19015a.pdf
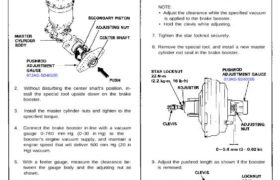
Pushrod Clearance Adjustment NOTE: Master cylinder pushrod-to-piston clearance must be checked and adjustments made, if necessary, before installing master cylinder. 1. Set the special tool on the master cylinder body; push in the center shaft until the top of it contacts with the end of the secondary piston by turning the adjusting nut. 07JAG-SD40100 2. […]
nsxb19067a.pdf
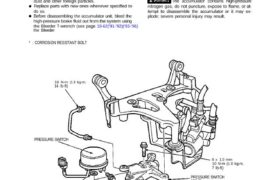
Accumulator/Pressure Switch Index/Torque CAUTION: Do not spill brake fluid on the car; it may damage the paint; if brake fluid does contact the paint, wash it off immediately with water. To prevent spills, cover the hose jpints with rags or shop towels. Clean all parts in brake fluid and air dry; blow out all passages […]
nsxb19069a.pdf
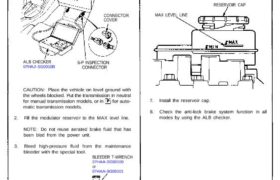
Bleeding Air Bleeding with ALB Checker 1. Disconnect the 6-P inspection connector (PNK) from the connector cover located under the glove box, and connect the 6-P inspection connector to the special tool. CONNECTOR COVER ALB CHECKER 07HAJ – SG0010B 6-P INSPECTION CONNECTOR CAUTION: Place the vehicle on level ground with the wheels blocked. Put the […]
nsxb19019a.pdf
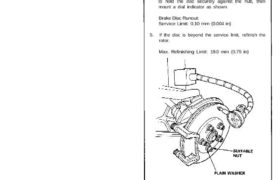
Rear Brake Disc Run-Out Inspection 1. Raise each side of the car, and support it on safety stands (see page 1-6 through 1-8). Remove the rear wheels. 2. Remove the brake pads (see page 19-17). 3. Inspect the disc surface for grooves, cracks, and rust. Clean the disc thoroughly and remove all rust. 4. Use […]
nsxb19061a.pdf
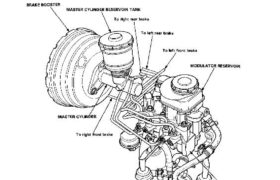
Hydraulic System Hydraulic Connections CAUTION: Do not spill brake fluid on the car; it may damage the paint; if brake fluid does contact the paint, wash it off immediately with water. Attachments nsxb19061a (54 kB)
nsxe19061a.pdf
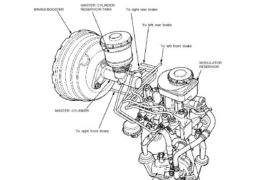
Hydraulic System Hydraulic Connections CAUTION: Do not spill brake fluid on the car; it may damage the paint; if brake fluid does contact the paint, wash it off immediately with water. BRAKE BOOSTER MASTER CYLINDER RESERVOIR TANK To right rear brake To left rear brake To left front brake MASTER CYLINDER To right front brake […]