Category: Driveshafts
nsxb16015a.pdf
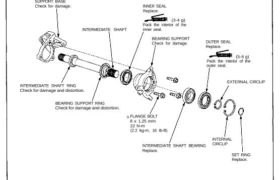
Index/Inspection CAUTION: • The bearing support and support base are made of aluminum. Be careful not to damage them when servicing. • The bearing support and support base are fitted and must be replaced as an assembly. Corrosion resistant bolt/nut SUPPORT BASE Check for damage. INNER SEAL Replace. (3-4 g) Pack the interior of the […]
nsxb16006a.pdf
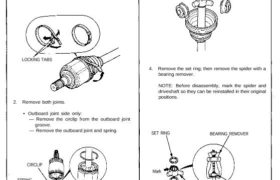
Driveshafts Disassembly 1. To remove the boot band, pry up the locking tabs with screwdriver, and raise the end of the band. NOTE: Carefully clamp the driveshaft in a vise with soft jaws. CAUTION: Take care not to damage the boots. LOCKING TABS 2. Remove both joints. • Outboard joint side only: — Remove the […]
nsxb16007a.pdf
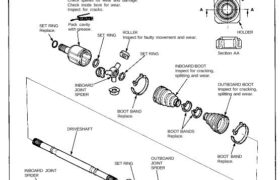
Inspection : Thoroughly pack the inboard joint and outboard joint with joint grease included in the new joint boot set. Grease Quantity: NOTE: Mark the rollers and roller grooves during disassembly to ensure proper positioning during reassembly. Spline direction INBOARD JOINT Check splines for wear and damage. Check inside bore for wear. Inspect for cracks. […]
nsxb16008a.pdf
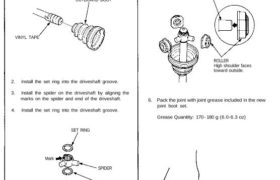
Driveshafts Reassembly Outboard joint side NOTE: Wrap the splines with vinyl tape to prevent damage to the boot. 1. Install the outboard boot to the driveshaft, then remove the vinyl tape. OUTBOARD BOOT VINYL TAPE 2. Install the set ring into the driveshaft groove. 3. Install the spider on the driveshaft by aligning the marks […]
nsxb16013a.pdf
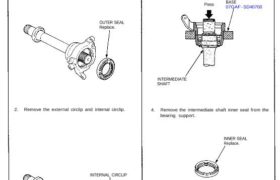
Disassembly CAUTION: The bearing support and support base are made of aluminum. Be careful not to damage them when servicing. 1. Remove the intermediate shaft outer seal from the bearing support. OUTER SEAL Replace. 2. Remove the external circlip and internal circlip. INTERNAL CIRCLIP EXTERNAL CIRCLIP 3. Press the intermediate shaft out of the shaft […]
nsxb16012a.pdf
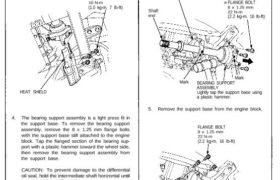
Intermediate Shaft Replacement 1. Drain the oil from the transmission (see section 13 M/T or section 14 A/T). 2. Remove the right driveshaft assembly (see page 16-3). 3. Remove the heat shield. Corrosion resistant bolt/nut FLANGE BOLT 6 x 1.0 mm 10 N-m (1.0 kg-m, 7 Ib-ft) HEAT SHIELD 4. The bearing support assembly is […]
nsxb16003a.pdf
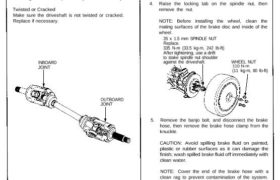
Driveshafts Removal INSPECTION Driveshaft Boot Check the boots on the driveshaft for cracks, damage, leaking grease and loose boot bands. If any damage is found, replace the boot. Spline Looseness Turn the driveshaft by hand, and make sure the splines and joints are not excessively loose. If damage is found, replace the joints if necessary. […]
nsxb16002a.pdf
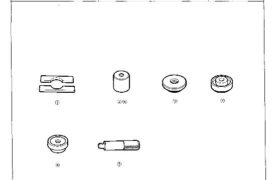
Special Tools 16-13, 16-14, 16-16, 16-17 16-16 16-16 16-16 16-17 16-14 16-14, 16-16, 16-17 Main Menu Table of Contents Special Tools Number Tool Number Description Qty Page Reference CD O7GAF—SD407OO Hub Dis/Assembly Base 2 16-13, 16-14, 16-16, 16-17 ® 07GAF-SE00200 Hub Assembly Guide Attachment 1 16-16 © O7GAD—PG40100 Oil Seal Driver 1 16-16 @ 07JAD—SH301OA […]
nsxb16016a.pdf
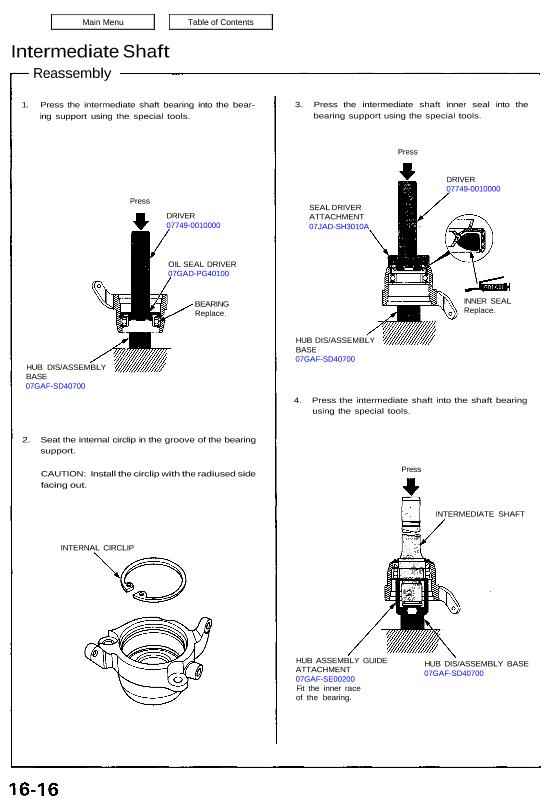
Intermediate Shaft Reassembly 1. Press the intermediate shaft bearing into the bear- ing support using the special tools. Press DRIVER 07749-0010000 OIL SEAL DRIVER 07GAD-PG40100 BEARING Replace. HUB DIS/ASSEMBLY BASE 07GAF-SD40700 2. Seat the internal circlip in the groove of the bearing support. CAUTION: Install the circlip with the radiused side facing out. INTERNAL CIRCLIP […]