Category: Engine Block
nsxb07003a.pdf
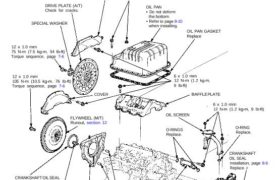
Engine Block Illustrated Index Lubricate all internal parts with engine oil during reassembly. NOTE: • Apply liquid gasket to the mating surfaces of the left side cover and oil pump case before install- ing them. • Use liquid gasket, part No. 08718-0001. If the bottom of the oil pan is deformed, it should be repaired […]
nsxb07009a.pdf
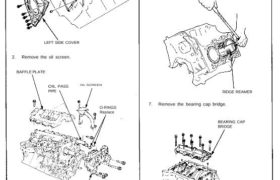
Piston/Connecting Rod Assemblies and Crankshaft Removal 1. Remove the left side cover. LEFT SIDE COVER 2. Remove the oil screen. BAFFLE PLATE OIL PASS OIL SCREEN PIPE O-RINGS Replace OIL PUMP 3. Remove the baffle plate. 4. Remove the oil pass pipe and joint. 5. Remove the oil pump. 6. If you can feel a […]
nsxb07012a.pdf
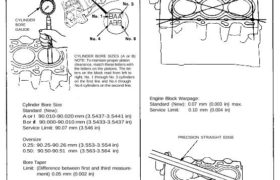
Cylinder Block Inspection 1. Measure wear and taper in directions X and Y at three levels in each cylinder as shown. CYLINDER BORE SIZES (A or B) NOTE: To maintain proper piston clearance, match these letters with the letters on the pistons. The let- ters on the block read from left to right, No. 1 […]
nsxb07014a.pdf
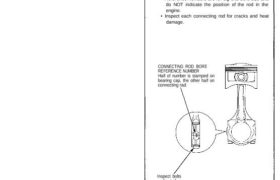
Connecting Rods Selection Each rod is sorted into one of four tolerance ranges (from 0 to 0.024 mm, in 0.006 mm increments) depen- ding on the size of its big end bore. It’s then stamped with a number (1, 2, 3 or 4) indicating that tolerance. You may find any combination of 1, 2, 3 […]
nsxb07007a.pdf
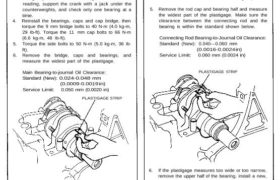
Main Bearings Clearance 1. To check main bearing-to-journal oil clearance, remove the main caps and bearing halves. 2. Clean each main journal and bearing half with a clean shop towel. 3. Place one strip of plastigage across each main jour- nal. NOTE: If the engine is still in the car when you bolt the main […]
nsxb07015a.pdf
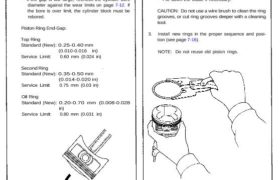
Piston Rings End Gap 1. Using a piston, push a new ring into the cylinder bore 15 – 20 mm (0.6 – 0.8 in) from the bottom. 2. Measure the piston ring end-gap with a feeler gauge: • If the gap is too small, check to see if you have the proper rings for your […]
nsxb07018b.pdf
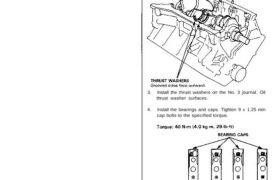
Crankshaft Installation Before installing the crankshaft, apply a coat of engine oil to the main bearings and rod bearings. 1. Insert bearing halves in the engine block and con- necting rods. 2. Lower the crankshaft into the block. 3. Install the thrust washers on the No. 3 journal. Oil thrust washer surfaces. 4. Install the […]
nsxb07013b.pdf
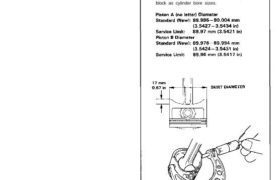
Piston/Connecting Rod Assemblies Inspection 1. Check the piston for distortion or cracks. NOTE: If cylinder is bored, an oversized piston must be used. 2. Measure piston diameter at a point 17 mm (0.67 in) from the bottom of the skirt. NOTE: There are two standard-size pistons (A = no letter and B). The letter is […]
nsxb07002a.pdf
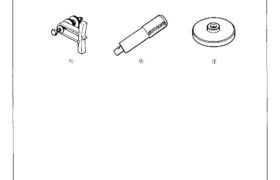
Special Tools 7-6 7-18 7-18 Mam Menu Table of Contents Special Tools 1 (¿j Ref. No. Tool Number Description Qty Page Reference G) 07LAB — PV00100 Ring Gear Holder 1 7—6 or 07924 — PD20003 ® 07749 — 0010000 Driver ‘I 7-18 ® 07948 — 5300101 Driver Attachment 1 7-18 G:) Attachments nsxb07002a (31 kB)
nsxb07011a.pdf
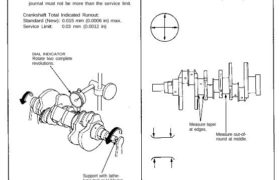
Crankshaft Inspection • Clean the crankshaft oil passages with pipe cleaners or a suitable brush. • Check the keyway and threads. Alignment • Measure runout on all main journals to make sure the crank is not bent. • The difference between measurements on each journal must not be more than the service limit. Crankshaft Total […]